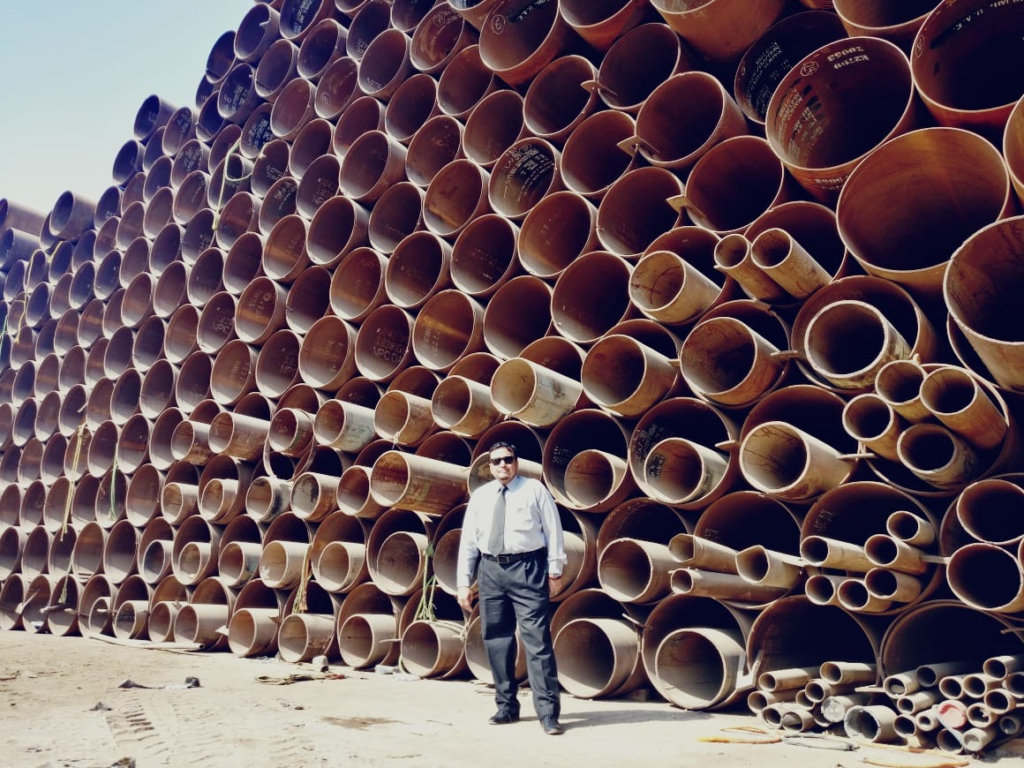
Common Problems With Flanges And How To Fix Them
Flanges are important components used to join pipes, valves, and other equipment in various systems. While they are generally durable and reliable, several issues can arise over time, leading to leaks, improper sealing, or performance failures. Identifying these problems early on and addressing them quickly can prevent costly repairs and system downtime. Finding the right flanges supplier in UAE can also help avoid some common flange-related issues.
Leaking seals:
One of the most common issues with flanges is leaking at the sealing area. This can occur due to improper installation, wear and tear, or an unsuitable gasket material. To fix this issue, inspect the gasket and flange surface for signs of damage or contamination. Replace any worn-out gaskets with appropriate materials that match the system’s requirements. Ensure that the flange is torqued properly, as over-tightening or under-tightening can also cause leaks.
Misalignment:
Misalignment occurs when the flange faces do not align correctly during installation, leading to uneven pressure distribution and possibly causing leaks. To fix misalignment, ensure that the flanges are positioned properly before tightening the bolts. Use alignment tools to check the positioning of the flanges and ensure that they are parallel and centered. Additionally, consider using flexible gaskets to compensate for minor misalignments.
Corrosion:
Corrosion is a significant concern, especially for flanges used in harsh environments or with corrosive substances. Over time, this can weaken the material and affect the flange’s ability to form a proper seal. To prevent corrosion, select corrosion-resistant materials, such as stainless steel or alloy-based flanges, suitable for the environment. Regular maintenance, including cleaning and inspecting the flanges, can also help detect early signs of corrosion before it becomes a major issue.
Over-tightening or under-tightening bolts:
Improper torque on flange bolts can lead to several issues, such as leaks or even flange damage. Over-tightening bolts can deform the flange or cause excessive stress on the sealing surface, while under-tightening can result in a poor seal. To avoid this, always follow the manufacturer’s torque specifications for the flange bolts. Use a calibrated torque wrench to ensure the proper amount of torque is applied during installation.
Incorrect flange size or type:
Using the wrong flange size or type for a particular application can lead to leaks, damage, or system inefficiency. It’s essential to choose the correct flange that matches the pipe size, pressure, and temperature requirements. Consult with your flanges supplier to ensure that the chosen flange is compatible with your system’s specifications.