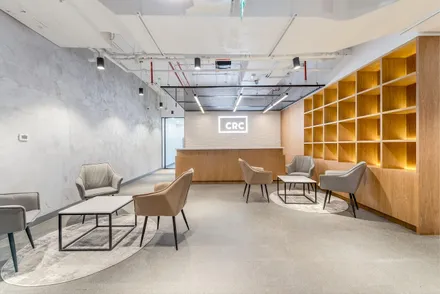
The Best Way To Optimize Warehouse Space Efficiently
Optimizing warehouse space is essential for improving productivity, reducing costs, and improving overall operational efficiency. By implementing effective strategies, you can increase the use of available space and streamline warehouse Al Quoz operations. Find here the best ways to optimize warehouse space efficiently.
Conduct a space audit:
Start with a thorough evaluation of your current warehouse layout and storage systems. Identify underutilized areas and assess how space is being used. A space audit will help you understand where improvements can be made.
Define goals:
Set clear goals for your warehouse optimization project. Whether it’s increasing storage capacity, improving workflow, or reducing operational costs, having defined objectives will guide your efforts and measure success. Also, increase vertical space by using tall storage racks and shelves. This approach increases storage capacity and also frees up floor space for other operations. Ensure that the racks are safely accessible with appropriate lifting equipment.
Use pallet racking systems:
Pallet racking systems are efficient for storing bulk items. They allow for easy access and organization of inventory. Choose the right type of racking system (e.g., selective, drive-in, push-back) based on your specific needs and inventory characteristics. Mobile shelving units can significantly increase storage density. These systems, which include rolling or track-mounted shelves, allow you to compactly store items and access them when needed, reducing wasted aisle space.
Implement ABC analysis:
Classify inventory using ABC analysis to consider storage based on item turnover rates. Place high-turnover (A) items in easily accessible locations, while low-turnover (C) items can be stored in less accessible areas. This strategy reduces handling time and optimizes space usage.
Utilize inventory management software:
Adopt advanced inventory management software to track and manage stock levels efficiently. These systems can provide real-time data, automate reordering processes, and help in optimizing storage locations based on demand patterns.
Design efficient layouts:
Design your warehouse layout to minimize travel time and streamline workflows. Place frequently accessed items near packing and shipping areas. Use clear signage and labeling to guide workers and reduce search times.
Divide the warehouse into zones for different activities such as receiving, storage, picking, packing, and shipping. Designating specific areas for each activity minimizes congestion and improves operational flow.